Transform your homebrewing cleaning routine with CIP (Clean-in-Place) systems designed for home brewers. Discover professional-grade cleaning techniques, equipment recommendations, and cost-effective solutions for maintaining pristine brewing equipment without disassembly.
Clean-in-Place (CIP) systems represent the pinnacle of brewing equipment sanitation, offering homebrewers a professional-grade approach to maintaining spotless fermentation vessels, kettles, and piping. While traditionally reserved for commercial breweries, modern CIP technology has evolved to meet the needs of serious home brewers seeking efficiency, consistency, and superior cleaning results.
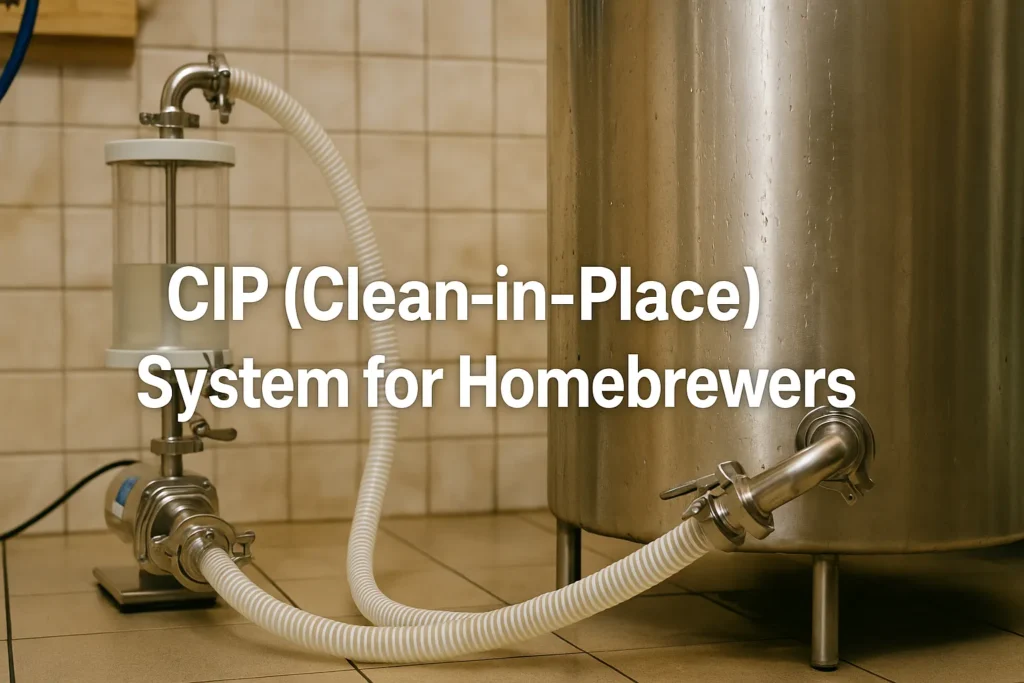
Understanding CIP Systems in Homebrewing
CIP systems automate the cleaning process by circulating heated cleaning solutions through brewing equipment without requiring disassembly or manual scrubbing. This technology relies on four fundamental principles known as the Sinner’s Circle: Time, Action (mechanical force), Chemical concentration, and Temperature (TACT). By balancing these elements, CIP systems achieve superior sanitation compared to traditional hand-cleaning methods.
The core advantage of CIP technology lies in its ability to reach areas that manual cleaning cannot access effectively. Complex internal geometries, tight spaces around cooling coils, and intricate valve assemblies receive consistent cleaning coverage through pressurized spray patterns and chemical circulation.
The Science Behind CIP Effectiveness
Modern CIP systems operate on proven scientific principles that commercial breweries have relied upon for decades. The mechanical action generated by high-pressure spray patterns creates turbulent flow that physically removes organic residues and mineral deposits. Chemical cleaning agents, when heated to optimal temperatures (typically 140-170°F), break down protein chains and dissolve stubborn soils that resist cold water cleaning.
Temperature control emerges as perhaps the most critical factor in CIP effectiveness. Heated cleaning solutions dramatically improve solubility and cleaning capability compared to room temperature alternatives. Professional brewing operations maintain precise temperature monitoring throughout the CIP process to ensure consistent results.
The chemical concentration aspect involves selecting appropriate cleaning agents for specific soil types. Alkaline cleaners like PBW (Powdered Brewery Wash) excel at removing organic compounds, proteins, and hop resins, while acid cleaners tackle mineral deposits and beer stone formation.
Essential Components of a Homebrewing CIP System
CIP Pumps: The Heart of Your System
Selecting the right pump represents the most crucial decision in CIP system design. For homebrewing applications (less than 20 gallons), you typically need a Chugger pump or equivalent 7 GPM pump, while larger systems require higher-capacity pumps.
Pump Requirements for Effective CIP:
Vessel Size | Recommended Pump | Flow Rate | Pressure |
---|---|---|---|
5-15 gallons | Chugger Standard | 7 GPM | 25-30 PSI |
15-30 gallons | Chugger Max | 17 GPM | 40-50 PSI |
30+ gallons | Commercial Grade | 25+ GPM | 60+ PSI |
Temperature considerations prove critical when selecting CIP pumps. Most standard submersible pumps handle temperatures up to 100-120°F, limiting their effectiveness with heated cleaning solutions. Many homebrewers find the lower maximum temperature to be problematic for optimal CIP performance.
Professional-grade solutions include hot water circulation pumps designed for elevated temperatures, though these command higher prices. Liberty Pumps and similar manufacturers offer models capable of handling the heat and flow requirements necessary for effective CIP operation.
CIP Spray Balls and Cleaning Heads
Spray ball selection directly impacts cleaning effectiveness and system performance. CIP spray balls require water at 25-30 PSI to work effectively, with most poor performance stemming from insufficient pressure.
Types of CIP Spray Devices:
Static Spray Balls: Fixed-position devices with drilled hole patterns that create multiple spray jets. These represent the most economical option but require higher flow rates to achieve adequate cleaning coverage.
Rotating Spray Balls: Combine static ball reliability with rotational movement for enhanced coverage. Their heavier design permits higher flow rates than most static spray balls, resulting in more effective cleaning.
Rotary Spray Heads: Generate high-impact cleaning action through curved and straight slots that emit fanned jets in swirling patterns. These devices excel in larger vessels with heavy soiling conditions.
Installation Considerations: Many homebrewers insert spray balls through existing ports, using PVC tubing and o-rings for secure positioning. This approach provides flexibility while maintaining effective spray coverage throughout the vessel.
Chemical Selection for Homebrewing CIP
Alkaline Cleaners form the foundation of most CIP programs. PBW Cleaner effectively removes thick, difficult, and caked-on organic soils while serving as a safe substitute for caustic soda cleaners. Professional brewers appreciate PBW’s ability to clean equipment that cannot be reached with brushes or sponges through soaking and circulation.
Recommended Concentrations:
- Fermenters and tanks: 3/4 ounce per gallon
- Kettles and brew vessels: 1-2 ounces per gallon
- Heavy soiling: Up to 3 ounces per gallon
Acid Cleaners address mineral deposits and beer stone formation. Acid cleaners primarily break down minerals and help keep stainless steel passivated and protected from corrosion. Five Star Acid #5 represents a popular choice for homebrewing applications.
Caustic Cleaners provide professional-level cleaning power for serious applications. Liquid Line Cleaner from Five Star contains 38% caustic blend, recommended at 2oz/gallon for brew kettles and lines at 160-180°F. However, caustic cleaners require proper safety equipment and training.
CIP System Design for Homebrewers
Basic CIP Circuit Design
Effective CIP systems create closed-loop circulation patterns that maximize contact time and mechanical action. A typical setup involves connecting a pump to the bottom drain and running hoses up to the CIP head, allowing for complete recirculation.
Essential Circuit Components:
- Supply pump for solution circulation
- Spray device (ball or head) for mechanical action
- Return path for solution recovery
- Temperature control system
- Chemical dosing capability
Advanced CIP Configurations
Heated CIP Systems provide superior cleaning performance through temperature control. Floating immersion heaters with temperature controllers maintain CIP solution temperature during operation. These systems typically require 1800-watt heaters with appropriate temperature controllers for effective operation.
Multi-Vessel CIP allows cleaning multiple fermenters or vessels sequentially. Three-way valves enable operators to draw cleaning solutions from one position and recirculate from vessel bottoms, providing flexibility for larger operations.
Safety Considerations in CIP Design
Chemical Safety represents the primary concern in CIP operations. Professional caustic chemicals require heavy health and safety protocols, proper safety gear, and COSHH processes. Homebrewers should carefully evaluate their comfort level with industrial-strength chemicals versus gentler alternatives.
Pressure Safety becomes critical with high-pressure CIP systems. Proper pressure relief valves, secure fittings, and regular equipment inspection prevent dangerous failures. Never exceed manufacturer-specified pressure ratings for spray devices or vessels.
Temperature Safety involves both equipment protection and operator safety. Heated cleaning solutions can cause pump cavitation and equipment damage if temperatures exceed design specifications.
Building Your First CIP System
DIY CIP System Construction
Budget-Friendly Approach: Harbor Freight pumps can provide adequate pressure for spray ball operation, though careful selection is required for temperature and chemical compatibility. Many successful homebrewers start with utility pumps and upgrade as their systems evolve.
Component Selection Strategy:
- Start with your largest vessel to determine pump requirements
- Choose spray devices based on vessel geometry and access
- Plan for heated operation from the beginning
- Design for expansion to accommodate future vessels
Construction Tips: Building CIP systems with available materials proves entirely feasible, using diaphragm pumps, inline heaters, and strategic valve placement. Many homebrewers successfully construct effective systems using dishwasher heating elements and automotive pumps.
Commercial CIP Solutions
Turnkey Systems offer plug-and-play convenience for homebrewers preferring professional solutions. Companies like SS Brewtech provide complete CIP packages sized for homebrewing applications, though at premium prices.
Professional Consultation benefits complex installations or multi-vessel operations. Chemical companies specializing in brewing can help develop customized cleaning and safety programs, ensuring optimal results and regulatory compliance.
CIP vs Traditional Cleaning Methods
Effectiveness Comparison
CIP Advantages:
- Consistent cleaning coverage
- Reduced labor requirements
- Better access to hard-to-reach areas
- Temperature control capability
- Chemical concentration control
Traditional Cleaning Benefits:
- Visual verification of cleanliness
- Lower equipment investment
- Simpler process control
- Better for heavy soil removal
Cost-Benefit Analysis
Initial Investment: CIP systems require significant upfront costs, including pumps, spray devices, heating systems, and control equipment. Basic systems start around $200-300, while professional setups can exceed $1000.
Operating Costs: CIP systems may use more chemicals and energy compared to simple soaking methods, but save considerable labor time and improve consistency.
Time Savings: Professional CIP operations typically complete cleaning cycles in 30-90 minutes, depending on soil load and system complexity. This represents significant time savings for brewers managing multiple vessels.
Challenges and Limitations in Homebrewing CIP
Common CIP Problems
Insufficient Pressure: Typical CIP balls require more pressure than standard homebrewing pumps can generate, leading to poor performance. This fundamental limitation affects many homebrewing CIP attempts.
Spray Ball Clogging: Small spray ball orifices can become clogged with grain particles or debris, requiring frequent maintenance. Pre-filtering cleaning solutions helps prevent this issue.
Temperature Control: Maintaining optimal cleaning temperatures throughout the cycle challenges many homebrewing systems lacking sophisticated heating control.
When CIP May Not Be Worth It
CIP is designed for things like hard piping and massive vessels that few homebrewers will ever have. For equipment that can be easily disassembled and manually cleaned, traditional methods may prove more practical and cost-effective.
Small Vessel Considerations: Vessels under 10 gallons may not justify CIP investment, as manual cleaning remains quick and effective. For smaller vessels, CIP becomes more hassle than it’s worth.
Advanced CIP Techniques and Optimization
Multi-Stage CIP Protocols
Professional CIP programs typically involve multiple cleaning stages:
- Pre-rinse: Hot water removal of gross soils
- Alkaline wash: Organic soil removal with heated PBW or caustic
- Intermediate rinse: Chemical removal and pH neutralization
- Acid wash: Mineral deposit and beer stone removal
- Final rinse: Complete chemical removal
- Sanitization: Final pathogen elimination
CIP Monitoring and Validation
Temperature Monitoring: CIP circuit return headers record and monitor temperatures to ensure heat reaches the entire system. Proper temperature control proves essential for effective cleaning.
Chemical Concentration Control: Conductivity sensors and timed doses monitor chemical concentration in closed-loop systems. This ensures adequate cleaning power while preventing waste.
Cleaning Validation: Visual inspection and microbial testing, such as ATP tests, ensure cleanliness and sanitation standards have been met. Documentation supports quality control and regulatory compliance.
Maintenance and Troubleshooting
CIP System Maintenance
Pump Maintenance: Regular inspection of seals, impellers, and housing prevents premature failure. Chemical compatibility verification ensures long-term operation with brewing chemicals.
Spray Device Care: Spray balls may stick in the same spot due to bearing issues or debris accumulation. Regular disassembly and cleaning maintains optimal performance.
Heating System Service: Descaling heating elements and checking temperature sensors prevents performance degradation and safety issues.
Common Troubleshooting Issues
Poor Spray Pattern: Insufficient pressure or clogged orifices reduce cleaning effectiveness. Verify pump output and clean spray devices regularly.
Temperature Loss: Inadequate insulation or oversized heating systems cause temperature control problems. Insulating vessels and upgrading heating capacity often resolves these issues.
Chemical Carryover: Insufficient rinsing leaves chemical residues that affect beer flavor. Extended rinse cycles and conductivity monitoring ensure complete chemical removal.
Future of CIP in Homebrewing
Technology Trends
Smart CIP Systems incorporate automated controls, remote monitoring, and data logging capabilities. These systems provide consistent results while reducing operator involvement.
Eco-Friendly Solutions focus on reduced water usage, energy efficiency, and biodegradable chemicals. Environmental consciousness drives innovation in CIP technology.
Modular Designs allow homebrewers to start with basic systems and add capabilities over time. This approach reduces initial investment while providing upgrade paths.
CIP System Specifications and Recommendations
Pump Selection Guide
Entry-Level Systems (5-15 gallons):
- Chugger Standard Pump: 7 GPM, 25 PSI
- Harbor Freight Utility Pumps: Budget option with limited temperature capability
- Pool/spa pumps: Higher pressure, chemical resistance
Mid-Range Systems (15-30 gallons):
- Chugger Max: 17 GPM, 40-50 PSI
- Liberty Pumps: Professional temperature rating
- Custom diaphragm pumps: High pressure, temperature capability
Professional Systems (30+ gallons):
- Sanitary centrifugal pumps: Food-grade construction
- Variable frequency drives: Pressure and flow control
- Integrated heating: Steam or electric options
Chemical Program Recommendations
Basic Two-Stage Program:
- Alkaline Cycle: PBW at 1-2 oz/gallon, 140-160°F, 20-30 minutes
- Sanitization: Star San or similar no-rinse sanitizer
Advanced Three-Stage Program:
- Alkaline Cycle: PBW or caustic cleaner, 140-170°F, 30 minutes
- Acid Cycle: Acid #5, 140-160°F, 20 minutes
- Sanitization: PAA or other professional sanitizer
Investment Analysis and ROI
Cost Breakdown
Basic CIP System:
- Pump: $100-300
- Spray ball: $30-80
- Fittings and hoses: $50-100
- Total: $180-480
Professional CIP System:
- High-capacity pump: $300-800
- Rotating spray head: $100-300
- Heating system: $200-500
- Control system: $100-400
- Total: $700-2000
Return on Investment
Time Savings: CIP systems reduce cleaning time from 45-60 minutes to 10-15 minutes of active work. For brewers cleaning multiple vessels weekly, this represents significant time savings.
Consistency Benefits: Automated cleaning reduces infection risk and improves beer quality consistency. The value of preventing infected batches justifies CIP investment for many serious homebrewers.
Equipment Longevity: Proper CIP protocols extend equipment life by preventing mineral buildup and corrosion. This benefit particularly applies to expensive stainless steel fermenters and complex valve assemblies.
For homebrewers seeking professional-grade cleaning capabilities, CIP systems offer compelling advantages despite significant initial investment. The technology transforms cleaning from a labor-intensive chore into an automated process, freeing brewers to focus on recipe development and brewing technique refinement.
However, success requires careful planning, appropriate component selection, and realistic expectations about system capabilities and limitations. CIP represents an evolution in homebrewing practices, bringing commercial brewery techniques within reach of dedicated home brewers willing to invest in advanced equipment and procedures.
For more information about building your ultimate home brewery setup, visit Brew My Beer for comprehensive guides, equipment reviews, and expert brewing advice tailored to home brewers at every experience level.
About the Author
John Brewster is a passionate homebrewer with over a decade of experience experimenting with different beer styles. After working at three craft breweries and winning several regional homebrew competitions, John now dedicates his time to developing innovative recipes and teaching brewing techniques. His specialty lies in creating unique flavor profiles by combining traditional brewing methods with unexpected ingredients. When not tending to his five fermenters, John enjoys pairing his creations with artisanal cheeses and hosting tasting sessions for friends and family.
Email: john.brewster@brewmybeer.online