Transform your brewing operation with intelligent automated grain mill hopper design that delivers consistent grain flow, reduces manual intervention, and maximizes milling efficiency for professional-quality results every batch.
The evolution from manual grain milling to automated grain mill hopper design represents a quantum leap in homebrewing precision and efficiency. Modern brewing operations demand consistent grain crush quality, predictable flow rates, and minimal operator intervention to achieve professional results. An intelligently designed automated hopper system eliminates the guesswork from grain preparation while dramatically improving batch-to-batch consistency.
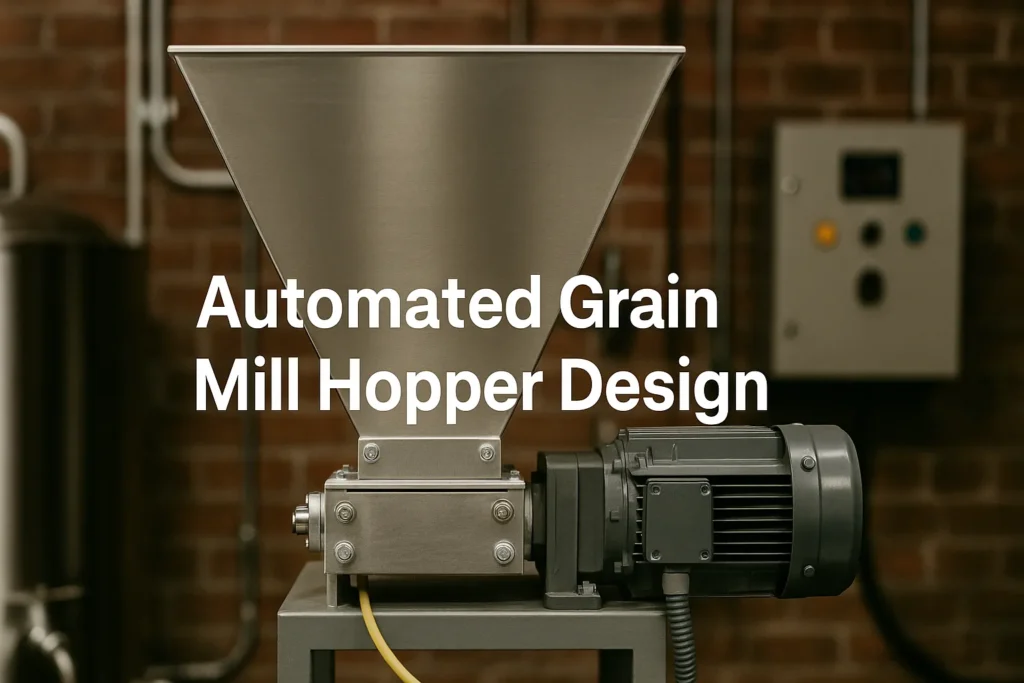
Bottom Line: Automated grain mill hopper systems reduce milling time by 40-60% while improving crush consistency and eliminating common flow problems like bridging and uneven distribution. Professional designs cost $200-800 to implement versus $2,000+ for commercial alternatives.
Traditional gravity-fed hoppers suffer from numerous limitations including inconsistent flow rates, grain bridging in corners, and the need for constant operator attention during milling. Modern automated solutions address these challenges through sophisticated sensor integration, motorized agitation systems, and intelligent control algorithms that ensure optimal grain presentation to mill rollers.
Fundamentals of Automated Hopper Engineering
Successful automated grain mill hopper design requires understanding the complex interplay between grain flow dynamics, mechanical systems, and control automation. Grain behaves as a granular material with unique flow characteristics that vary significantly based on moisture content, particle size distribution, and storage conditions.
Grain Flow Physics and Design Principles
The foundation of effective hopper design lies in understanding granular flow mechanics. Grain exhibits both cohesive and non-cohesive behavior depending on environmental conditions, requiring adaptive design strategies that accommodate varying flow characteristics.
Critical Flow Parameters:
- Angle of repose (typically 28-35° for malted barley)
- Bulk density variations (32-48 lbs/ft³ depending on grain type)
- Moisture content effects on flow characteristics
- Particle size distribution impact on bridging tendency
- Static friction coefficients between grain and hopper materials
Professional grain handling systems utilize sophisticated sensors and control algorithms to monitor these parameters continuously, adjusting flow rates and agitation patterns to maintain optimal milling conditions.
Modern Sensor Integration Technologies
Contemporary automated hoppers incorporate multiple sensor technologies to provide real-time monitoring and control capabilities. These systems transform traditional passive hoppers into intelligent grain management platforms that optimize performance automatically.
Sensor Type | Measurement Capability | Typical Accuracy | Integration Complexity |
---|---|---|---|
Load Cell Arrays | Weight/Volume | ±0.1% | Moderate |
Ultrasonic Level | Distance/Volume | ±1mm | Low |
Capacitive Proximity | Grain Presence | Binary | Low |
Vibration Analysis | Flow Rate/Blockage | ±2% | High |
Infrared Temperature | Grain Condition | ±0.5°C | Low |
Advanced systems combine multiple sensor inputs to create comprehensive grain flow management solutions. BinMaster level sensors exemplify professional-grade monitoring systems adapted for smaller brewing applications, providing the foundation for sophisticated automation strategies.
Engineering Design Methodologies
Successful automated hopper implementation requires systematic engineering approaches that address mechanical design, control system integration, and operational requirements. Professional designs follow established methodologies that ensure reliable operation and easy maintenance.
Mechanical System Architecture
The mechanical foundation determines overall system reliability and performance characteristics. Modern designs emphasize modular construction, standardized interfaces, and robust materials that withstand the demanding brewing environment.
Primary Structural Elements:
- Reinforced hopper shell with optimized geometry
- Motorized agitation assemblies for flow enhancement
- Variable-speed drive systems for precise control
- Integrated weighing platforms for inventory management
- Automated cleaning and maintenance access points
Professional hopper designs incorporate features learned from commercial grain processing equipment scaled appropriately for homebrewing applications. The key lies in maintaining commercial-grade reliability while controlling costs through intelligent material selection and manufacturing approaches.
Flow Control Mechanisms
Automated flow control represents the most critical aspect of hopper design, directly impacting grain consistency and milling efficiency. Modern systems employ multiple complementary approaches to ensure reliable grain delivery under varying conditions.
Advanced Flow Enhancement Technologies:
- Servo-controlled gate assemblies for precise flow regulation
- Pneumatic agitation systems for bridging prevention
- Vibrating platforms for consistent grain movement
- Smart sensors for blockage detection and automatic clearing
- Variable-frequency drives for optimized motor control
The integration of these systems requires careful consideration of control algorithms that balance flow rate optimization with gentle grain handling. Excessive agitation can damage grain husks, while insufficient movement leads to inconsistent flow patterns.
Automation Control Systems
The intelligence behind automated hoppers lies in sophisticated control systems that integrate sensor inputs, process algorithms, and mechanical outputs into seamless operation. Modern microcontroller platforms provide the computational power necessary for real-time optimization.
Control System Components:
- Programmable logic controllers (PLCs) for industrial reliability
- Human-machine interfaces (HMIs) for operator interaction
- Distributed sensor networks for comprehensive monitoring
- Wireless communication systems for remote operation
- Data logging capabilities for process optimization
Professional systems utilize established industrial protocols and standards, ensuring compatibility with existing brewing automation infrastructure. The modular approach enables incremental system expansion as brewing operations grow.
Advanced Sensor Technologies and Integration
Modern automated hoppers rely heavily on sensor fusion to create intelligent grain management systems. Multiple sensor types work together to provide comprehensive monitoring and control capabilities that surpass human operators in both speed and consistency.
Weight-Based Monitoring Systems
Load cell integration provides the most accurate method for monitoring grain inventory and flow rates. Professional systems employ multiple load cells in strategic locations to compensate for off-center loading and dynamic forces during operation.
Load Cell Configuration Options:
- Single-point systems for simple installations
- Multi-point arrays for improved accuracy
- Compression designs for high-capacity applications
- Tension configurations for suspended hoppers
- Strain gauge alternatives for cost-sensitive applications
The implementation of hopper scale systems adapted from commercial grain processing provides laboratory-grade accuracy in smaller brewing applications. Proper installation and calibration procedures ensure long-term measurement reliability.
Proximity and Level Detection
Non-contact sensing technologies provide reliable detection of grain levels and flow conditions without interfering with normal operation. These sensors complement weight-based systems by providing rapid response to changing conditions.
Non-Contact Sensor Applications:
- Ultrasonic ranging for continuous level monitoring
- Capacitive proximity for binary presence detection
- Infrared beam-break systems for flow rate measurement
- Radar technologies for challenging environments
- Optical systems for grain quality assessment
The selection of appropriate sensor technologies depends on specific application requirements, environmental conditions, and accuracy specifications. Professional installations often combine multiple sensor types to provide redundant monitoring capabilities.
Flow Rate and Blockage Detection
Maintaining consistent flow rates requires sophisticated monitoring systems that detect both gradual changes and sudden blockages. Modern sensors provide real-time feedback that enables immediate corrective action before problems affect grain quality.
Flow Monitoring Technologies:
- Vibration analysis for mechanical condition assessment
- Acoustic monitoring for blockage detection
- Optical flow measurement for rate verification
- Differential pressure sensing for airflow systems
- Temperature monitoring for motor protection
Advanced algorithms process these sensor inputs to distinguish between normal variations and problematic conditions, automatically initiating corrective actions when necessary.
Motorized Agitation and Flow Enhancement
Automated hoppers require active flow enhancement systems to ensure consistent grain presentation to mill rollers. These systems must provide sufficient agitation to prevent bridging while avoiding grain damage that could affect brewing performance.
Agitation System Design Principles
Effective agitation systems balance multiple competing requirements including energy efficiency, noise levels, maintenance requirements, and grain handling gentleness. Professional designs optimize these parameters through careful mechanical design and control system integration.
Agitation Mechanism Options:
- Rotating paddles for gentle grain movement
- Vibrating platforms for mechanical stimulation
- Pneumatic systems for contactless agitation
- Auger assemblies for positive grain transport
- Oscillating gates for flow regulation
The selection of appropriate agitation mechanisms depends on grain characteristics, hopper geometry, and operational requirements. Many professional systems incorporate multiple complementary technologies to ensure reliable operation under varying conditions.
Motor Selection and Control
The heart of automated agitation systems lies in properly selected and controlled drive motors. Modern variable-frequency drives enable precise speed control and soft-start capabilities that protect both mechanical components and grain quality.
Motor Technology Considerations:
- Servo motors for precise positioning control
- Stepper motors for repeatable positioning
- AC induction motors for robust continuous operation
- DC motors for simple speed control
- Pneumatic actuators for explosive-proof applications
Professional installations typically favor servo motor systems due to their combination of precision, reliability, and integration capabilities. The investment in quality drive systems pays dividends through improved consistency and reduced maintenance requirements.
Intelligent Flow Algorithms
Modern control systems employ sophisticated algorithms that adapt agitation patterns based on real-time sensor feedback and learned system characteristics. These systems continuously optimize performance while minimizing energy consumption and component wear.
Algorithm Components:
- Predictive flow modeling based on grain characteristics
- Adaptive speed control responding to sensor feedback
- Preventive blockage detection and clearing
- Energy optimization through demand-based operation
- Maintenance scheduling based on usage patterns
The implementation of machine learning techniques enables systems to improve performance over time, learning optimal operating parameters for different grain types and environmental conditions.
Construction Materials and Durability
The demanding brewing environment requires careful material selection to ensure long-term reliability and food safety compliance. Professional automated hoppers utilize materials and finishes specifically chosen for their performance characteristics and maintenance requirements.
Food-Grade Material Requirements
All surfaces in contact with grain must meet stringent food safety requirements while providing the durability necessary for continuous operation. Modern materials science provides numerous options that balance performance, cost, and safety considerations.
Approved Material Options:
- 304/316 stainless steel for maximum durability
- Food-grade aluminum alloys for weight reduction
- High-density polyethylene (HDPE) for cost-effectiveness
- Polypropylene composites for chemical resistance
- Glass-filled nylon for structural applications
The selection process must consider not only initial cost but also long-term maintenance requirements, cleaning compatibility, and potential contamination risks. Professional installations typically favor stainless steel despite higher initial costs due to superior longevity and easy maintenance.
Surface Treatments and Finishes
Proper surface treatments significantly impact both grain flow characteristics and cleaning effectiveness. Professional systems utilize specialized finishes that optimize performance while minimizing maintenance requirements.
Surface Treatment Options:
- Electropolished stainless steel for smoothness
- Anodized aluminum for corrosion protection
- Food-grade powder coatings for cost-effectiveness
- Plasma treatments for enhanced flow characteristics
- Specialized non-stick coatings for difficult materials
The investment in proper surface treatments pays dividends through improved flow consistency, easier cleaning, and reduced maintenance requirements over the system lifetime.
Corrosion Resistance and Longevity
Brewing environments present unique corrosion challenges including moisture, temperature variations, and chemical exposure during cleaning operations. Professional designs address these challenges through material selection, protective treatments, and design features that minimize exposure.
Corrosion Prevention Strategies:
- Proper material selection for environment
- Protective coatings and treatments
- Design features that promote drainage
- Ventilation systems to control humidity
- Regular maintenance and inspection protocols
Long-term reliability depends on comprehensive corrosion prevention strategies implemented during initial design and maintained throughout system life.
Control System Integration and Automation
The intelligence of modern automated hoppers lies in sophisticated control systems that integrate multiple subsystems into cohesive, optimized operation. These systems must balance performance optimization with reliability and ease of use.
Programmable Logic Controller (PLC) Implementation
Professional automated hoppers utilize industrial-grade PLCs that provide the reliability and expandability necessary for demanding brewing applications. These systems offer sophisticated programming capabilities while maintaining the ruggedness required for continuous operation.
PLC System Advantages:
- Industrial-grade reliability and durability
- Standardized programming languages and interfaces
- Extensive input/output capabilities for sensor integration
- Network connectivity for system integration
- Comprehensive diagnostic and troubleshooting tools
The selection of appropriate PLC platforms depends on system complexity, expansion requirements, and integration needs with existing brewing automation systems.
Human-Machine Interface (HMI) Design
Effective operator interfaces balance comprehensive functionality with intuitive operation. Modern HMI systems provide touchscreen interfaces that enable easy system monitoring and control while maintaining industrial durability.
HMI Design Principles:
- Intuitive navigation and control layouts
- Real-time system status and alarm displays
- Historical data trending and analysis
- Recipe storage and recall capabilities
- Remote access and monitoring options
Professional HMI designs incorporate established human factors engineering principles to ensure effective operation under the demanding conditions of active brewing operations.
Network Integration and Data Management
Modern brewing operations increasingly rely on integrated data management systems that provide comprehensive process monitoring and optimization capabilities. Automated hoppers must integrate seamlessly with these broader systems.
Integration Capabilities:
- Ethernet/IP networking for real-time data exchange
- OPC-UA protocols for standardized connectivity
- Cloud-based data storage and analysis
- Mobile device interfaces for remote monitoring
- Integration with existing brewery management systems
The investment in proper network integration provides long-term benefits through improved process optimization and operational efficiency.
Safety Systems and Fail-Safe Mechanisms
Automated grain handling systems present unique safety challenges that require comprehensive protection strategies. Professional designs incorporate multiple safety layers to protect both personnel and equipment under all operating conditions.
Personnel Protection Systems
The combination of moving mechanical components and electrical systems requires comprehensive personnel protection measures. Professional installations follow established safety standards while maintaining operational efficiency.
Safety System Components:
- Emergency stop systems accessible from all operator positions
- Light curtains and presence sensors for area protection
- Interlocked guards for mechanical component access
- Lockout/tagout systems for maintenance operations
- Warning systems for automated operation modes
The implementation of comprehensive safety systems protects personnel while ensuring compliance with applicable safety regulations and insurance requirements.
Equipment Protection Mechanisms
Automated systems require sophisticated protection mechanisms to prevent damage from operating abnormalities and component failures. These systems must detect problems quickly and respond appropriately to minimize damage.
Equipment Protection Features:
- Motor overload protection and thermal monitoring
- Mechanical jam detection and automatic shutdown
- Sensor failure detection and backup systems
- Power quality monitoring and protection
- Preventive maintenance scheduling and alerts
Professional systems incorporate redundant protection mechanisms to ensure reliable shutdown under abnormal conditions while minimizing false alarms that interrupt normal operation.
Fault Detection and Recovery
Modern control systems provide sophisticated fault detection capabilities that identify problems before they cause significant damage or product loss. These systems must balance sensitivity with stability to provide reliable operation.
Fault Management Capabilities:
- Predictive maintenance alerts based on operating data
- Automatic recovery from transient faults
- Comprehensive fault logging and analysis
- Remote diagnostic capabilities for service support
- Graceful degradation modes for continued operation
The investment in comprehensive fault management systems pays dividends through reduced downtime, lower maintenance costs, and improved overall system reliability.
Performance Optimization and Efficiency
Automated hopper systems provide numerous opportunities for performance optimization that can significantly improve overall brewing efficiency. These optimizations often provide rapid return on investment through reduced labor requirements and improved consistency.
Flow Rate Optimization
Optimal grain flow rates balance milling speed with grain quality preservation. Modern control systems enable precise flow rate control that adapts to varying grain characteristics and milling requirements.
Optimization Parameters:
- Variable speed control matching mill capacity
- Adaptive flow rates based on grain characteristics
- Surge prevention to maintain consistent quality
- Energy optimization through demand-based operation
- Predictive control based on recipe requirements
Professional systems utilize sophisticated algorithms that continuously optimize flow rates while maintaining grain quality and system efficiency.
Energy Efficiency Considerations
Modern automated systems incorporate numerous energy efficiency features that reduce operating costs while maintaining performance. These features often provide significant long-term cost savings that justify initial system investments.
Energy Efficiency Features:
- Variable-frequency drives for motor control
- Demand-based operation to minimize idle power
- High-efficiency motors and drive systems
- Power factor correction for electrical efficiency
- Smart scheduling to optimize energy usage
The implementation of comprehensive energy efficiency measures provides both cost savings and environmental benefits throughout system life.
Maintenance Optimization
Automated systems enable sophisticated maintenance optimization strategies that reduce both planned and unplanned maintenance requirements. These strategies improve system reliability while controlling long-term operating costs.
Maintenance Optimization Strategies:
- Condition-based maintenance using sensor data
- Predictive maintenance algorithms
- Automated lubrication systems
- Component life tracking and replacement scheduling
- Remote monitoring for service optimization
Professional maintenance optimization provides significant cost savings while improving system reliability and operational efficiency.
Cost Analysis and Return on Investment
The financial justification for automated hopper systems depends on careful analysis of both initial costs and long-term benefits. Professional installations typically provide attractive returns through labor savings, improved consistency, and operational efficiency gains.
Initial Implementation Costs
Automated hopper systems require significant initial investments that must be carefully evaluated against expected benefits. Professional cost analysis considers both direct component costs and installation requirements.
Component Category | Cost Range | Percentage of Total |
---|---|---|
Mechanical Components | $400-800 | 35-45% |
Control Systems | $300-600 | 25-35% |
Sensors and Instrumentation | $200-400 | 15-25% |
Installation and Commissioning | $300-500 | 20-30% |
Training and Documentation | $100-200 | 8-12% |
Total system costs typically range from $1,300-2,500 for comprehensive automated hopper installations, depending on complexity and features included.
Operating Cost Reductions
Automated systems provide numerous operating cost reductions that accumulate over system life. These savings often justify initial investments within 1-3 years depending on operation scale and labor costs.
Operating Cost Benefits:
- Reduced labor requirements for grain handling
- Improved batch consistency reducing waste
- Lower maintenance costs through condition monitoring
- Energy savings through optimized operation
- Improved quality control reducing rework
Professional cost analysis considers all these factors to provide comprehensive return on investment calculations that support informed decision making.
Long-Term Value Proposition
The long-term value of automated hopper systems extends beyond direct cost savings to include operational improvements that enhance overall brewing capability and quality.
Long-Term Benefits:
- Improved product consistency and quality
- Enhanced production capacity and flexibility
- Reduced operator training requirements
- Better process documentation and traceability
- Increased operational flexibility and scalability
These benefits often provide value that exceeds direct cost savings, particularly for growing brewing operations that plan to increase production volume or complexity.
Troubleshooting and Maintenance Protocols
Effective maintenance strategies ensure long-term reliability while minimizing operating costs. Professional protocols address both preventive maintenance and troubleshooting procedures that maintain optimal performance.
Preventive Maintenance Schedules
Systematic preventive maintenance prevents problems before they occur while optimizing component life and system reliability. Professional schedules balance maintenance requirements with operational demands.
Maintenance Schedule Components:
- Daily visual inspections and basic cleaning
- Weekly lubrication and adjustment checks
- Monthly sensor calibration and testing
- Quarterly comprehensive system inspections
- Annual major component replacement and upgrades
The implementation of systematic maintenance protocols significantly extends system life while reducing unexpected failures and associated costs.
Common Issues and Solutions
Automated hopper systems present unique troubleshooting challenges that require systematic approaches for effective resolution. Professional troubleshooting protocols enable rapid problem identification and resolution.
Common System Issues:
- Sensor calibration drift affecting accuracy
- Mechanical wear causing performance degradation
- Control system faults disrupting operation
- Environmental factors affecting sensor performance
- Electrical problems causing intermittent operation
Comprehensive troubleshooting documentation enables effective problem resolution while minimizing downtime and service costs.
Performance Monitoring and Optimization
Continuous performance monitoring enables proactive maintenance and optimization that maintains peak system performance throughout its operational life.
Monitoring Parameters:
- Flow rate consistency and accuracy
- Energy consumption trends
- Component wear indicators
- Sensor performance metrics
- Control system response times
Professional monitoring systems provide early warning of developing problems while identifying optimization opportunities that improve overall performance.
Future Technologies and Innovations
The field of automated grain handling continues to evolve with new technologies that promise even greater automation, efficiency, and integration capabilities. Understanding these trends enables informed decisions about system investments and upgrade strategies.
Artificial Intelligence Integration
Machine learning and AI technologies offer unprecedented opportunities for system optimization and predictive maintenance. These technologies enable systems to learn optimal operating parameters and adapt to changing conditions automatically.
AI Application Areas:
- Predictive maintenance using pattern recognition
- Adaptive control algorithms that optimize performance
- Quality prediction based on sensor data
- Energy optimization through intelligent scheduling
- Fault prediction and prevention
The integration of AI technologies represents the next frontier in automated grain handling, offering performance improvements that justify ongoing technology investments.
Internet of Things (IoT) Connectivity
IoT technologies enable comprehensive remote monitoring and control capabilities that extend beyond traditional automation boundaries. These systems provide unprecedented visibility into system performance and operating conditions.
IoT Benefits:
- Remote monitoring and diagnostics
- Cloud-based data storage and analysis
- Mobile device interfaces for anywhere access
- Integration with broader facility management systems
- Advanced analytics and optimization capabilities
Professional IoT implementations provide significant operational advantages while enabling new service and support models that improve long-term system value.
Advanced Sensor Technologies
Emerging sensor technologies promise improved accuracy, reliability, and integration capabilities that enhance automated hopper performance. These technologies often provide capabilities previously available only in laboratory environments.
Emerging Sensor Technologies:
- Wireless sensor networks reducing installation costs
- Advanced imaging systems for quality assessment
- Non-invasive flow measurement technologies
- Environmental sensors for condition optimization
- Advanced diagnostic capabilities for predictive maintenance
The continuous evolution of sensor technologies provides ongoing opportunities for system enhancement and performance improvement.
Automated grain mill hopper design represents a transformative technology that elevates homebrewing operations to professional standards while maintaining cost-effectiveness and operational simplicity. The integration of modern sensors, control systems, and mechanical components creates intelligent grain handling systems that consistently outperform traditional manual approaches.
The key to successful implementation lies in understanding the fundamental principles of grain flow dynamics, sensor integration, and control system design. Professional installations that follow established engineering practices provide reliable operation, excellent return on investment, and the foundation for future operational expansion.
Modern automated hoppers deliver measurable improvements in consistency, efficiency, and operational flexibility that justify their investment through both direct cost savings and enhanced brewing capabilities. The technology has matured to the point where homebrewing operations can access professional-grade automation at reasonable costs.
Looking forward, emerging technologies including artificial intelligence, IoT connectivity, and advanced sensors promise even greater capabilities and value. Automated hopper systems designed with future expansion in mind provide platforms for continuous improvement and adaptation to evolving brewing requirements.
For brewers committed to excellence and efficiency, automated grain mill hopper systems provide the foundation for professional-quality operations that scale effectively while maintaining the precision and consistency demanded by modern brewing standards. The investment in proper automation pays dividends throughout the system lifecycle through improved performance, reduced operating costs, and enhanced brewing capabilities.
Whether upgrading existing manual systems or designing new brewing operations, automated hopper technology offers compelling advantages that justify careful consideration. The combination of proven technology, reasonable costs, and significant operational benefits makes automated grain handling an essential component of serious brewing operations.
For comprehensive resources and detailed implementation guidance, visit Brew My Beer for expert advice on advanced brewing automation and system design.
Author: Mark Kegman
Mark Kegman spent 15 years as a mechanical engineer before turning his analytical mind to brewing equipment. His methodical approach to testing and reviewing brewing gear has earned him a reputation for thorough, unbiased assessments. Mark maintains a fully equipped home brewery lab where he puts everything from budget starter kits to professional-grade systems through rigorous testing protocols. He’s particularly passionate about helping brewers find the best value equipment and innovative solutions for small-space brewing setups. His detailed comparison videos have amassed over 2 million views online.
Email: mark.kegman@brewmybeer.online