Build your own electric HERMS system with this comprehensive step-by-step guide. Learn professional temperature control techniques, safety protocols, and automation features for consistent brewing results every time.
Professional brewers have long relied on precise temperature control to create exceptional beers, and the electric HERMS system represents the pinnacle of homebrewing automation. A Heat Exchange Recirculating Mash System combines the precision of electric heating with the gentle heat transfer of water bath temperature control, offering homebrewers unprecedented consistency and control over their brewing process.
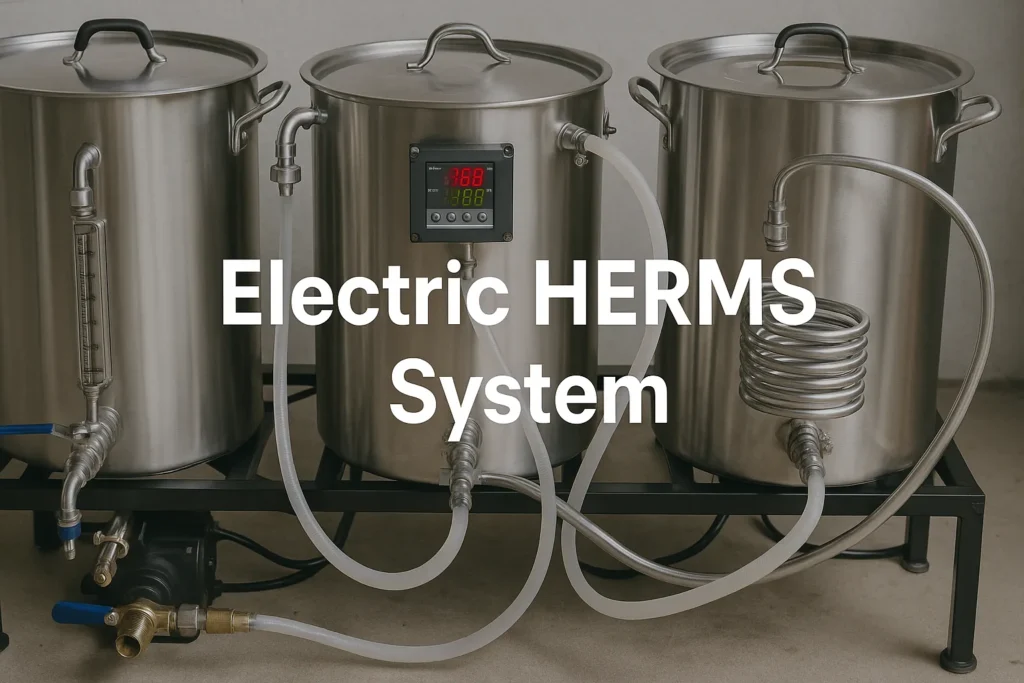
Key Takeaway: An electric HERMS system provides professional-grade temperature control for $800-1,500 compared to $5,000+ commercial alternatives, delivering precise mash temperature regulation within ±1°F while enabling complex step-mash profiles impossible with traditional methods.
Unlike gas-fired systems that rely on manual flame adjustment or simple electric setups with direct heating, an electric HERMS system uses sophisticated PID temperature controllers to maintain water temperatures that gently heat the recirculating mash through a heat exchange coil. This indirect heating method prevents scorching, ensures even temperature distribution, and enables precise temperature ramping for complex brewing recipes.
Understanding Electric HERMS System Fundamentals
An electric HERMS system operates on the principle of indirect heat exchange, where heated water in the Hot Liquor Tank (HLT) transfers thermal energy to the mash through a submerged coil. The mash continuously recirculates from the bottom of the mash tun, through the heated coil, and returns to the top of the grain bed, creating a consistent temperature throughout the mash while clarifying the wort.
Core System Components
The electric HERMS configuration consists of five essential vessels and control systems working in harmony. The HLT contains both the heating element and the heat exchange coil, while precise temperature controllers manage the entire process automatically.
Component | Function | Typical Specifications |
---|---|---|
Hot Liquor Tank | Primary heating vessel | 15-20 gallons, electric element |
Mash/Lauter Tun | Grain bed container | 10-15 gallons, insulated |
Boil Kettle | Wort boiling vessel | 15-20 gallons, electric element |
HERMS Coil | Heat exchanger | 25-50 feet, 1/2″ stainless tubing |
Control Panel | Automation center | PID controllers, SSRs, pumps |
The beauty of electric HERMS lies in its automation capabilities. Temperature controllers monitor both the HLT water temperature and mash temperature, automatically adjusting heating elements to maintain precise setpoints. This enables complex step-mash profiles that would be nearly impossible to execute manually with traditional systems.
Advantages Over Alternative Systems
Electric HERMS systems offer significant advantages over both RIMS (Recirculating Infusion Mash System) and direct-fire systems. While RIMS systems heat the wort directly through electric elements, potentially causing localized overheating, HERMS provides gentle, even heating through water bath temperature control.
The thermal mass of the HLT water provides excellent temperature stability, preventing rapid temperature swings that can shock enzymes and affect conversion efficiency. Additionally, the electric heating elements provide precise, repeatable heat input that gas systems cannot match, enabling brewers to duplicate successful recipes with mathematical precision.
Essential Components and Materials
Building an electric HERMS system requires careful selection of components that work together seamlessly. Quality components ensure safety, reliability, and longevity while providing the precision control that makes these systems worthwhile investments.
Heating Elements and Power Requirements
The foundation of any electric brewing system lies in properly sized heating elements and electrical infrastructure. For most homebrewing applications, 5500-watt elements provide excellent performance for 10-15 gallon batches while remaining within typical residential electrical capacity.
Critical Safety Note: All electric brewing systems require proper GFCI protection and grounding. Never compromise on electrical safety – a properly installed system includes GFCI breakers, appropriate wire gauges (10 AWG for 30-amp circuits), and complete equipment grounding.
Ultra-low watt density (ULWD) elements distribute heat over larger surface areas, reducing the risk of wort caramelization or scorching. These elements typically feature folded or zigzag patterns that double the effective heating surface compared to standard water heater elements.
Temperature Control Systems
Modern PID controllers form the brain of electric HERMS systems, providing precise temperature control through sophisticated algorithms that learn system characteristics and respond predictively to temperature changes. Quality PID temperature controllers offer features like auto-tuning, programmable setpoints, and data logging capabilities.
Essential Control Features:
- RTD (PT100) temperature probes for accuracy within ±0.2°F
- Solid State Relays (SSRs) for silent, long-life switching
- Cycle time adjustment for optimal element control
- Alarm outputs for safety monitoring
- Multiple output options for heating and pump control
The control system must manage both heating elements independently while coordinating pump operation and safety interlocks. Professional-grade systems include element selector switches that prevent simultaneous operation of multiple high-power elements, avoiding electrical overload.
HERMS Coil Design and Installation
The heart of the heat exchange system, the HERMS coil, determines heat transfer efficiency and system response time. Longer coils provide more heat transfer surface area but increase pressure drop and wort volume, while larger diameter tubing reduces flow restriction but may require more HLT water volume.
Professional coils typically use 50 feet of 1/2-inch stainless steel tubing configured in a compact spiral that fits within standard 15-20 gallon kettles. The crossover design, where inlet and outlet connections emerge from opposite sides, provides installation flexibility and reduces stress on connections.
Step-by-Step Construction Process
Building an electric HERMS system requires methodical approach and attention to safety throughout the construction process. Professional results demand quality components, proper electrical work, and thorough testing before the first brew day.
Phase 1: Electrical Infrastructure and Control Panel
Begin construction with the electrical foundation, as this determines the system’s capabilities and safety. Design the control panel layout carefully, allowing adequate space for heat dissipation and future upgrades while maintaining clean, professional appearance.
Control Panel Construction Sequence:
- Cut and prepare the enclosure with proper hole sizing
- Install DIN rail and mount all control components
- Wire the low-voltage control circuits first
- Install high-voltage circuits with appropriate separation
- Add safety interlocks and emergency stops
- Test all circuits before energizing elements
Use appropriately rated components throughout – 30-amp SSRs for 5500-watt elements, proper heat sinks for thermal management, and industrial-grade switches and indicators. Quality terminal blocks simplify wiring and enable easy troubleshooting.
The main power disconnect should be easily accessible and clearly marked. Include both ammeter and voltmeter for system monitoring, and consider adding hour meters to track element usage for maintenance scheduling.
Phase 2: Vessel Preparation and Element Installation
Kettle modification requires precision drilling and careful attention to sealing and safety. Use proper hole saws and cutting lubricant to achieve clean holes that ensure watertight seals and proper element fit.
Element Installation Safety Protocol:
- Verify power disconnection before drilling
- Use appropriate PPE including safety glasses
- Deburr all holes to prevent cuts and ensure proper sealing
- Test all connections with multimeter before energization
- Verify proper grounding of all vessels
Install elements with proper gaskets and tightening sequences to prevent leaks. The element housing should be electrically bonded to the vessel for safety, and all electrical connections must be protected from moisture intrusion.
Consider element positioning carefully – elements should be positioned to avoid dead spots while remaining accessible for cleaning. In the HLT, ensure the HERMS coil doesn’t interfere with element operation or create hot spots.
Phase 3: Pumping and Recirculation Systems
The recirculation system moves wort from the mash tun through the HERMS coil and back to the grain bed. Proper pump selection and plumbing design ensure adequate flow rates while minimizing pressure drop and maintaining gentle handling of the wort.
Food-grade pumps rated for hot liquids provide reliable service in brewing applications. Magnetic drive pumps eliminate seal leakage concerns, while centrifugal designs handle particulates better than positive displacement types. Size pumps for 4-6 gallons per minute flow rates to ensure adequate heat transfer without excessive turbulence.
Plumbing and Flow Control
Install ball valves throughout the system to enable cleaning, maintenance, and operational flexibility. Use stainless steel fittings where possible, with food-grade silicone tubing for flexible connections. Include sight glasses or flow indicators to monitor system operation visually.
Critical Flow Path Components:
- Pump inlet filtration to prevent clogging
- Pressure relief valves for safety
- Cleaning connections for CIP (Clean-in-Place) capability
- Sample ports for quality monitoring
- Bypass valves for pump protection
Design the system with “first-in, last-out” principles where the first vessel to receive wort becomes the last to return it, ensuring balanced flow distribution and minimizing dead legs where wort might stagnate.
Advanced Control and Automation Features
Modern electric HERMS systems can incorporate sophisticated automation that rivals commercial brewery capabilities. These features improve consistency, reduce operator workload, and enable complex brewing processes that would be difficult to execute manually.
Programmable Mash Profiles
Advanced controllers support complex step-mash profiles with automated temperature ramping, hold times, and seamless transitions between mash steps. This capability enables brewers to optimize enzyme activity for specific beer styles while ensuring repeatable results.
Typical Step-Mash Sequence:
- Protein rest: 122°F for 20 minutes
- Saccharification: 152°F for 60 minutes
- Mash-out: 168°F for 10 minutes
- Automatic sparge water heating
Programming controllers for these profiles eliminates manual intervention while providing data logging for process verification and troubleshooting. Some systems integrate with brewing software for recipe management and batch tracking.
Safety Systems and Interlocks
Professional electric HERMS systems incorporate multiple safety layers to protect equipment and personnel. These systems monitor temperatures, pressures, and flow rates while providing automatic shutdown capabilities for abnormal conditions.
Essential Safety Features:
- High-temperature shutdown for element protection
- Low-flow detection for pump protection
- GFCI monitoring with automatic disconnection
- Emergency stop functions with manual reset
- Thermal overload protection for all motors
Consider implementing redundant temperature monitoring with independent high-limit controllers that can shut down heating elements if primary controllers fail. This approach, common in commercial systems, prevents costly equipment damage and potential safety hazards.
Data Logging and Process Monitoring
Modern brewing benefits from detailed process data that enables continuous improvement and troubleshooting. Digital controllers with logging capabilities capture temperature profiles, heating cycles, and operational parameters for later analysis.
Integration with smartphone apps or computer interfaces enables remote monitoring and control, allowing brewers to track progress without constant physical presence. This capability proves particularly valuable for long mash schedules or overnight processes.
System Sizing and Performance Optimization
Proper system sizing ensures adequate performance while avoiding unnecessary complexity and cost. Calculate heating requirements based on batch size, ambient conditions, and desired temperature ramp rates to specify appropriate element sizes and electrical infrastructure.
Heat Transfer Calculations
Heat transfer rates depend on temperature differential, coil surface area, and flow rates through the system. Larger temperature differences between HLT and mash provide faster heating but risk overshooting target temperatures, while smaller differences provide gentler control with slower response times.
Batch Size | HLT Element | HERMS Coil | Expected Ramp Rate |
---|---|---|---|
5 gallons | 3000W | 25 feet | 3-4°F/minute |
10 gallons | 5500W | 50 feet | 2-3°F/minute |
15 gallons | 5500W | 50 feet | 1-2°F/minute |
Factor in thermal losses from vessels, piping, and ambient conditions when calculating heating requirements. Well-insulated systems require less energy and provide more stable temperatures, improving both efficiency and control quality.
Flow Rate Optimization
Optimize recirculation rates to balance heat transfer efficiency with gentle wort handling. Higher flow rates improve heat transfer and temperature uniformity but increase pressure drop and may cause grain bed compaction or channeling.
Most systems operate effectively with 4-6 gallons per minute recirculation rates, providing adequate heat transfer while maintaining reasonable pressure drops. Monitor pressure differentials across the grain bed and adjust flow rates if excessive resistance develops.
Troubleshooting and Maintenance
Regular maintenance ensures reliable operation and extends system life while preventing costly failures during brewing sessions. Establish preventive maintenance schedules based on usage patterns and component specifications.
Common Issues and Solutions
Temperature Control Problems:
- Sluggish response: Check coil coverage, increase HLT setpoint differential
- Overshoot: Reduce PID gain, increase derivative time
- Oscillation: Tune PID parameters, check sensor placement
- Inaccurate readings: Calibrate sensors, verify probe placement
Flow and Pumping Issues:
- Reduced flow: Clean pump strainer, check for blockages
- Pump cavitation: Verify adequate inlet pressure, check for air leaks
- Inconsistent flow: Inspect check valves, verify proper priming
Electrical Problems:
- Element failure: Test resistance, inspect connections
- SSR failure: Check heat sink temperatures, verify input signals
- Control issues: Verify wiring, check supply voltages
Preventive Maintenance Schedule
After Each Use:
- Flush all lines with hot water
- Clean and sanitize pump and fittings
- Inspect electrical connections for corrosion
- Record operational parameters for trending
Monthly:
- Calibrate temperature sensors
- Test safety systems and interlocks
- Inspect heating elements for scaling
- Lubricate pump bearings if required
Annually:
- Replace pump seals and gaskets
- Test GFCI devices and electrical systems
- Descale heating elements and coils
- Update controller firmware if available
Cost Analysis and Return on Investment
Electric HERMS systems represent significant investments that pay dividends through improved beer quality, consistency, and brewing efficiency. Compare costs against commercial alternatives and factor in long-term benefits when evaluating system economics.
Construction Cost Breakdown
Component Category | Cost Range | Percentage of Total |
---|---|---|
Control Panel | $400-600 | 30-40% |
Heating Elements | $200-300 | 15-20% |
Vessels and Fittings | $300-500 | 25-35% |
Pumps and Plumbing | $200-350 | 15-25% |
HERMS Coil | $100-200 | 8-12% |
Total system costs typically range from $1,200-1,950 for complete 10-gallon capacity systems, compared to $5,000+ for equivalent commercial systems. Quality component selection and careful construction deliver professional results at homebrew prices.
Long-term Benefits
Beyond initial cost savings, electric HERMS systems provide ongoing advantages through improved brewing efficiency, reduced batch losses, and enhanced beer quality. Precise temperature control enables complex recipes and consistent results that command premium prices for commercial operations.
Energy efficiency improvements through better insulation and control optimization can reduce operating costs by 20-30% compared to less sophisticated systems. Automated operation reduces labor requirements while improving batch consistency and reducing the potential for human error.
Advanced Features and Future Upgrades
Modern electric HERMS systems provide excellent foundations for future enhancement and automation. Design systems with expansion capability to accommodate growing brewing ambitions and evolving technology.
Integration Opportunities
Consider integration with broader brewery management systems that handle inventory tracking, recipe management, and production scheduling. These systems increasingly support homebrewing scales while providing professional-grade capabilities.
Wireless connectivity enables remote monitoring and control through smartphone applications, allowing brewers to track progress and make adjustments without physical presence. Some systems support social media integration for sharing brewing progress and achievements.
Emerging Technologies
Advanced sensor technology continues to improve measurement accuracy while reducing costs. Wireless sensor networks eliminate wiring complexity while providing comprehensive process monitoring throughout the brewing system.
Artificial intelligence and machine learning capabilities increasingly appear in brewing applications, offering predictive maintenance, automatic recipe optimization, and quality prediction based on process parameters. These technologies promise to further automate brewing while improving consistency and reducing waste.
Professional Tips for Success
Successful electric HERMS construction requires attention to detail and commitment to quality throughout the build process. Learn from experienced builders and invest in proper tools and components for professional results.
Expert Construction Techniques
Use proper electrical techniques throughout – marine-grade connections resist corrosion, proper strain relief prevents wire damage, and appropriate conduit protects wiring from damage. Label all circuits clearly for easy troubleshooting and maintenance.
Take time for proper system commissioning before first use. Test all safety systems, calibrate all sensors, and verify proper operation under various conditions. Document all settings and procedures for future reference.
Operational Best Practices
Develop standard operating procedures that ensure consistent results while maintaining safety. Include startup sequences, normal operations, cleaning procedures, and emergency shutdown protocols.
Keep detailed brewing logs that capture both process parameters and sensory evaluation results. This data enables continuous improvement and helps identify correlations between process variations and beer quality.
Building an electric HERMS system represents a significant step toward professional brewing capabilities within the homebrewing environment. These systems provide unprecedented temperature control, automation capabilities, and brewing consistency that enable complex recipes and repeatable results.
Success requires careful planning, quality components, and attention to safety throughout the construction and operation phases. The investment in time and materials pays dividends through improved beer quality, operational efficiency, and brewing satisfaction.
For brewers ready to elevate their craft through precision temperature control and professional automation, electric HERMS systems provide the foundation for brewing excellence. The combination of electric heating precision and water bath temperature control delivers results that rival commercial brewing operations at a fraction of the cost.
Whether building a first automated system or upgrading existing equipment, electric HERMS technology offers the perfect balance of sophistication and accessibility. With proper construction and operation, these systems provide years of reliable service while enabling continuous improvement in brewing quality and consistency.
For additional resources and detailed component specifications, visit Brew My Beer for comprehensive guides and community support for advanced homebrewing projects.
Author: Ryan Brewtech
Ryan Brewtech bridges the gap between traditional brewing and cutting-edge technology. With a background in computer engineering and IoT development, Ryan designs automated brewing systems that improve consistency while maintaining craft quality. He specializes in data-driven brewing, using sensors and software to monitor and optimize every aspect of the brewing process. Ryan has developed several open-source brewing applications and affordable DIY automation solutions for homebrewers. He regularly tests new brewing gadgets and technologies, separating genuine innovations from marketing hype.
Email: ryan.brewtech@brewmybeer.online